Yet another project - one of my favorite types of instruments to work on - maybe because there are so many abused examples out there ?
This is a late 60's Gibson EB-3 bass - structurally very similar to a 68/69 EB-0 I recently finished and sold on Ebay, but thats been through some trials and mods over the years.
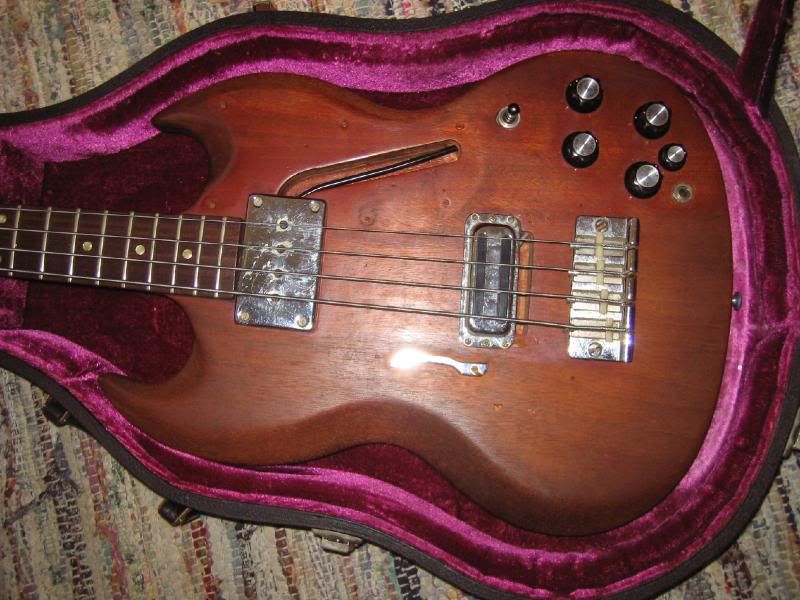
The mods are minor and reversible - notably, the bridge position mini-humbucker was replaced with a Rickenbacker "toaster" pickup from a '67 Rick 4005 bass - as were all the electronics and knobs. This was actually one of the primary motivations for me to acquire this bass - I coincidentally have a mid-60s Rick 4005 bass in pieces - missing the electronics and one pickup - lost pieces eventually recirculate to their rightful places - perhaps I have stumbled upon a very material expression of the eastern concept of karma - "guitarma ??"
The main "trial" this bass has been through - besides having its cherry finish stripped - is that like many Gibsons, it suffered a headstock break. Apparently this was repaired by laminating a 1/8" thick piece of mahogany on the back of the headstock. Also, the Gibson logo was removed and replaced with an approximation in mother of pearl and there was an extra hole to fill in the front of the body for the added Rickenbacker "blend" knob.
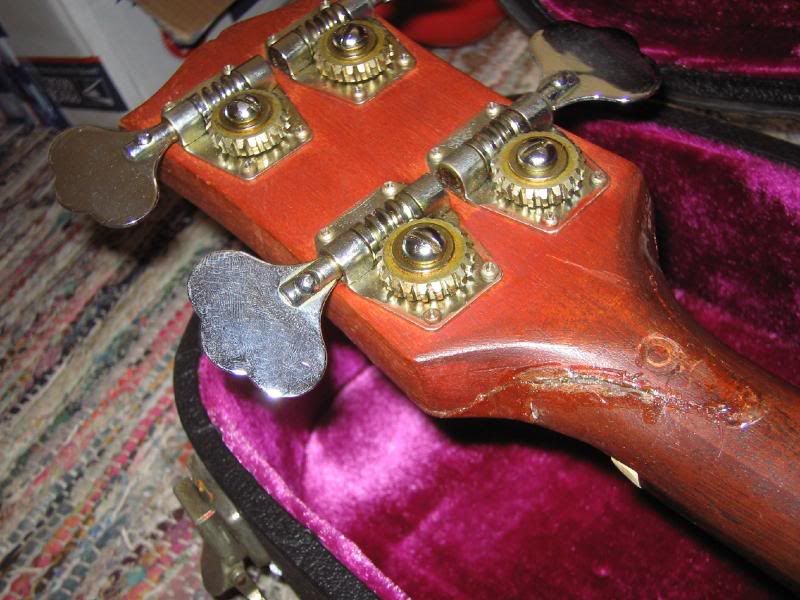
The bass also had a replacement metal (steel?) pickguard and control panel cover and a chromed finger rest.
On the plus side - the bass had the original neck humbucker, bridge, mute assembly, tuners and hard shell case - and outside of two finger wear spots on the front of the bass and the extra control hole, the body was in excellent condition. I have the correct Pat # baby humbucker for the bridge position, repro knobs and will make a new pickguard, backplate and thumbrest.
The two parts I dont have are the brass control cavity shield and the 4-position Variatone switch. But I'll keep looking or simply install an SG-style toggle.
The first step after disassembly was to take down the headstock to the proper thickness on a belt sander - taking care not to make it uneven or TOO thin. I left the last little bit of the laminated piece on and used a sanding block to even everything out. Not surprisingly, there was no serial number remaining. I also had to recarve the neck to headstock transition - using my 65 EB-0 as a guide - not too tricky.
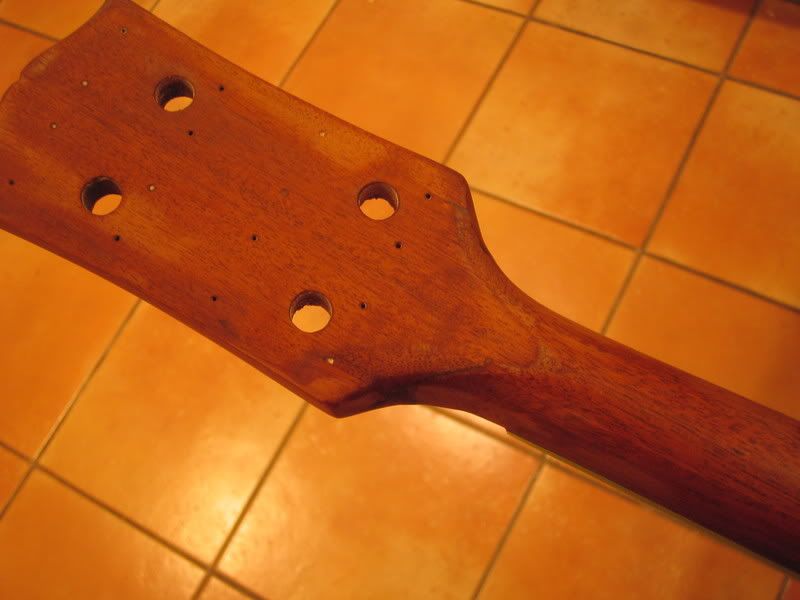
The headstock repair seemed very solid - no worries about it pulling apart - the laminated mahogany was an overkill type repair. And once everything was sanded down, there was nothing that a good solid color refin wouldn't cover up ! And I am very fond of Pelham Blue.
I plugged the control with a mahogany plug and then used some nitro based scratch filler on the deeper of the two wear marks and the control plug. This view is BEFORE sanding.
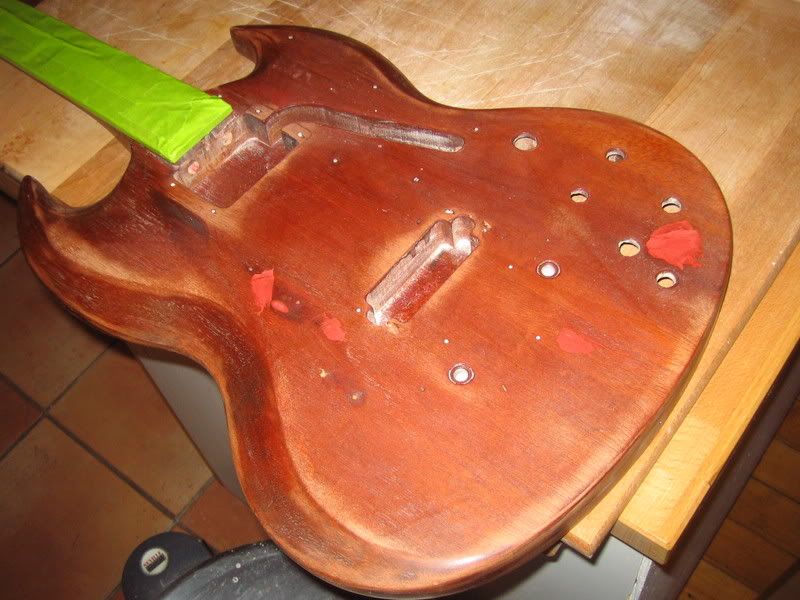
The body and neck were completely sanded and then grain filler was slopped on - and allowed to partly dry before I scrubbed off the excess. After drying overnight, I sanded the entire bass down again - using a sanding block, a random orbital sander and plain old sandpaper. I then sealed the filler with a good heavy coat of clear nitro sanding sealer - and the grain really "popped" after this treatment. I almost felt bad about covering that gorgeous wood up with blue paint ...
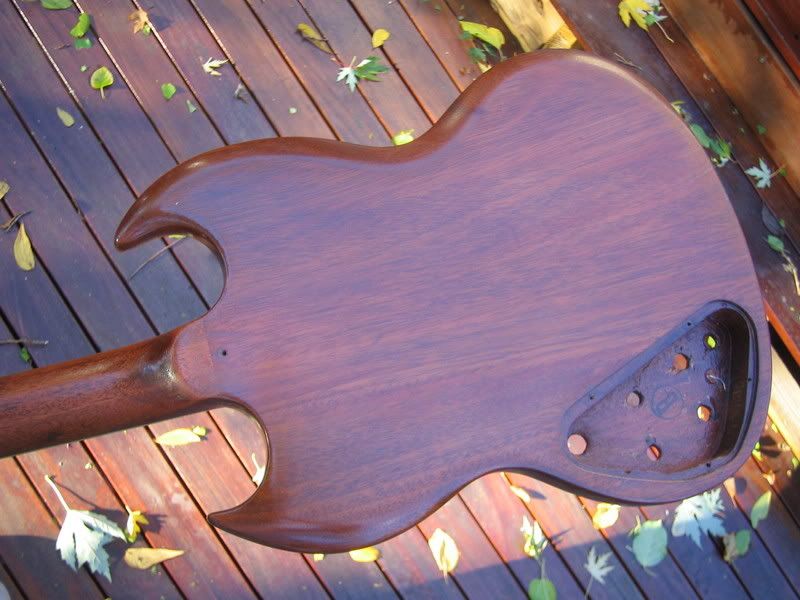
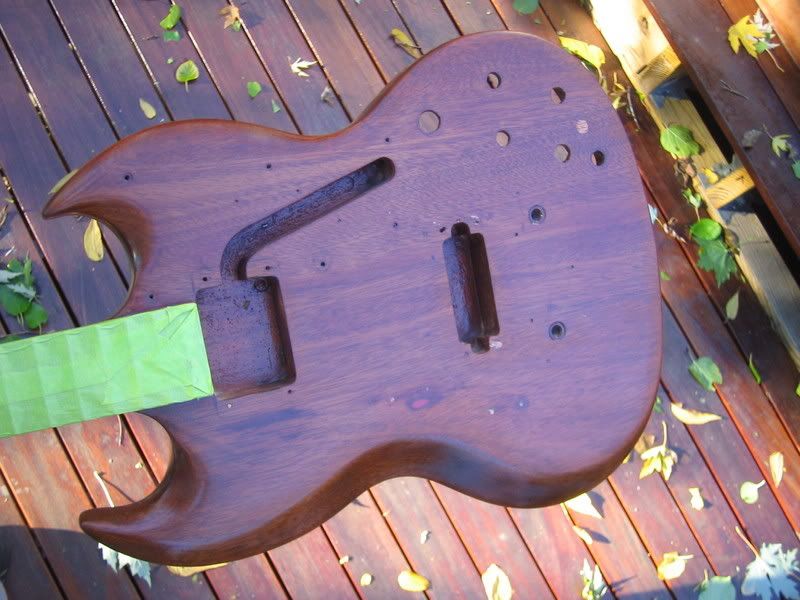
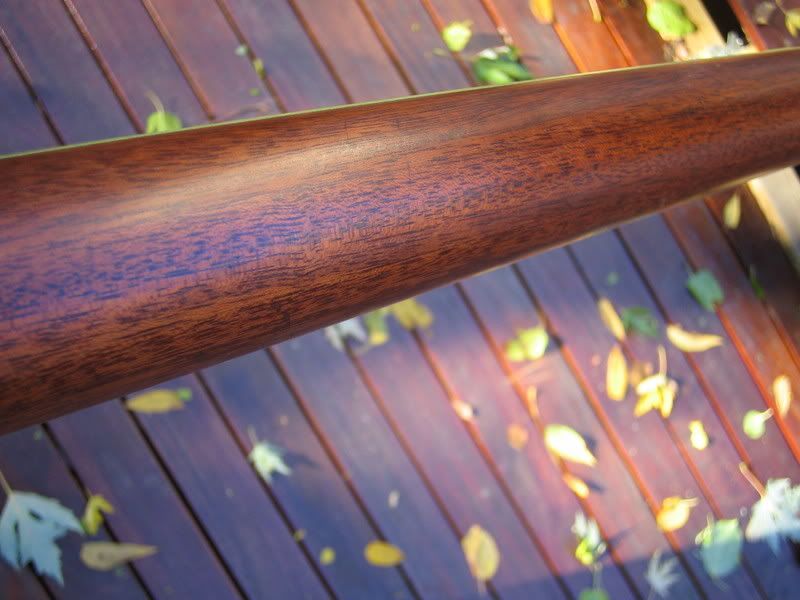
This is what a piece of mahogany with the grain properly filled should look like - notice that there is no filler on the surface of the wood - only in the grain, so that once a clear coat is applied, the wood has a mirror finish that still emphasizes the grain of the mahogany.
I used my Pelham Blue Melodymaker as a guide on matching the color - since the MM is heavily yellowed, I had to look for places it was well worn to get an idea of the original color - which is a surprisingly bright metallic blue, that of course appears green after 40 years of the top coat yellowing. I'll try to post a few closeups of the MM later - but meanwhile, here is the EB-3 with the first few color coats on.
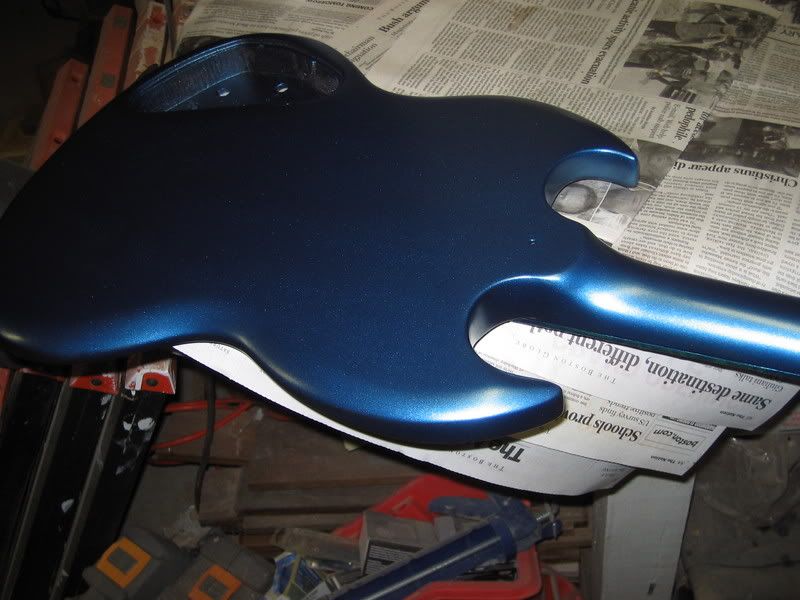
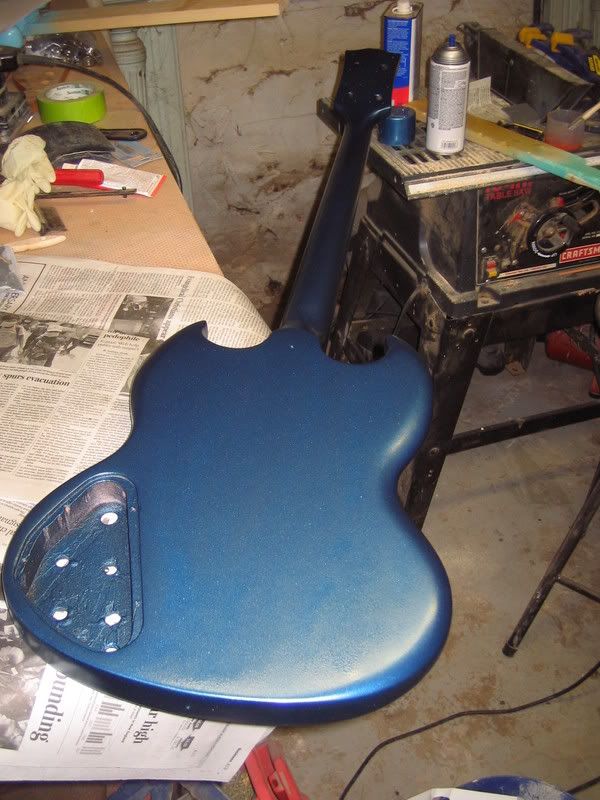
(added Oct. 24th, 10:30 am)
OK, here are a few pictures of the EB-3 compared to the original Pelham Blue finish, beat-to-hell Melodymaker guitar. Notice how the different light radically changes the appearance of the Pelham Blue - the pictures above were taken under my shop neon lights - the ones below were taken under low-power halogens.
The first picture is a close-up of one area on the MM where the top coat has worn off and left some of the original finish exposed - compare this to the picture above and you will see how close the two metallic blues are.
This guitar was played to death - lots of mojo.
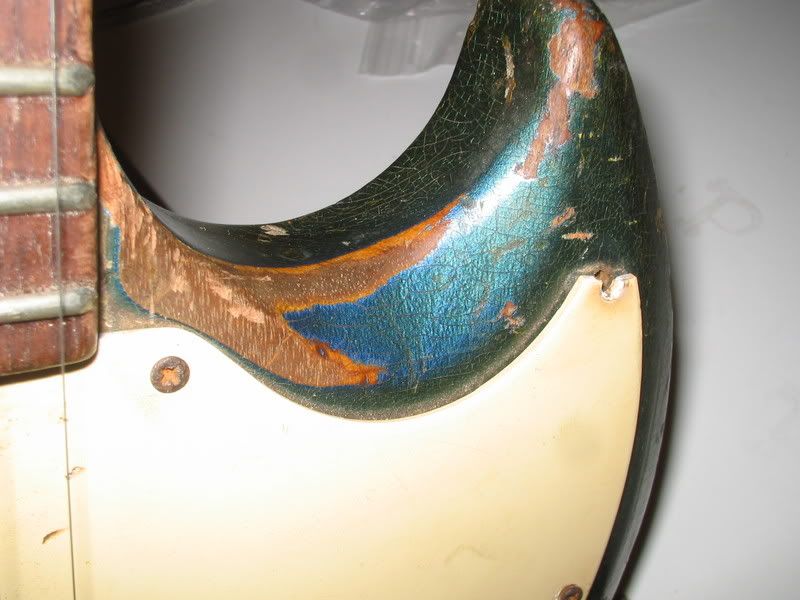
Then here is a pic of the EB-3 by itself (some parts just placed) and side by side with the MM. I'd have to do a lot of yellowing to match that color !!
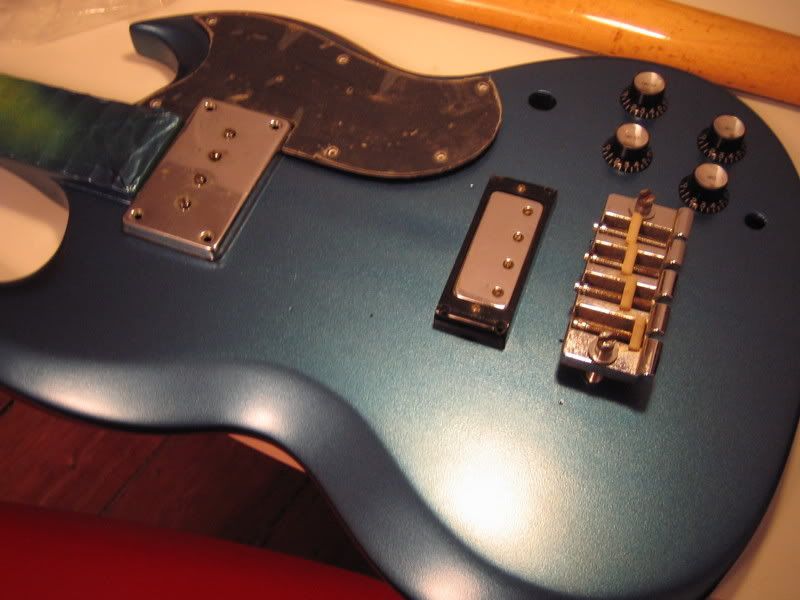
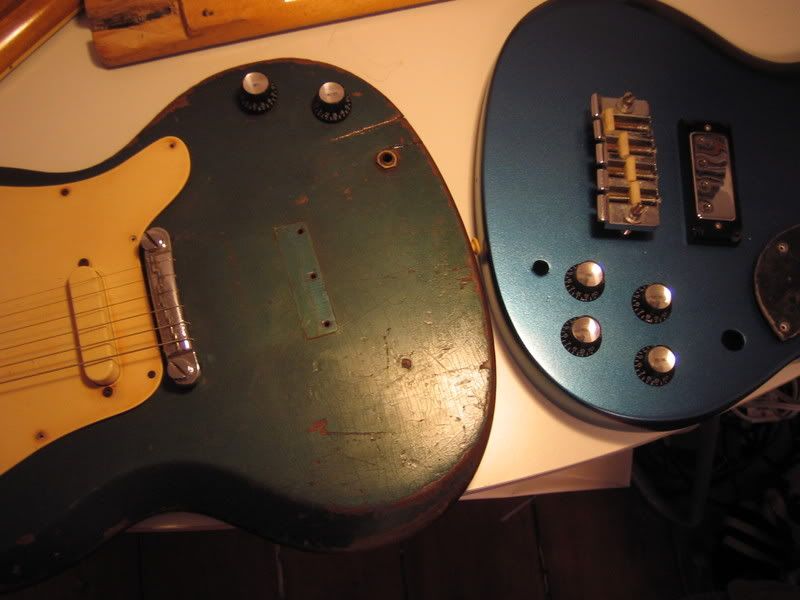
( Updated Oct. 26th, 11:30 PM)
OK - so I touched up the Pelham Blue - looked pretty much perfect, and then began applying a yellowed/ambered topcoat to start getting the EB-3 towards the proper aged green look. A tricky proposition to get a nice even color - but I made a good start - Sunday I'll try a lighter tinted coat and try to even out the back and get the front a little bit greener - and do the back of the headstock too!
A pic of the front of the bass - and then a picture of the neck with yellowing and headstock without yellowing to show the contrast.
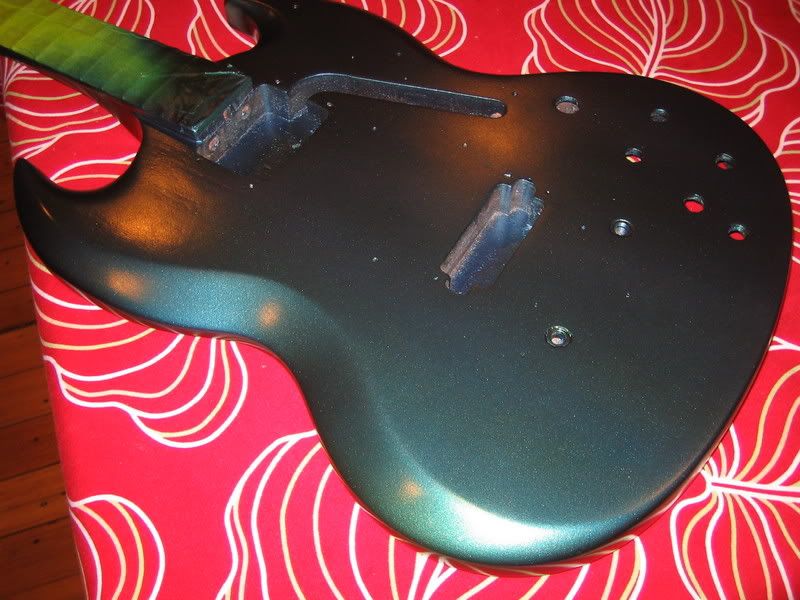
0 comments: